Aluminum Boat Fishing Rod Mounting Plates (jakeru's #8)
I welded some aluminum plate onto the gunwales ("side walls") of an aluminum boat last week. These 3/8" thick plates will be subsequently drilled and tapped by the customer for mounting a heavy downrigger style fishing rod setup, used for salmon fishing.
The gunwales of the boat were approximately 1/8" thick aluminum. Just below the aluminum, there were air tight cavities filled with foam (for buoyancy.) The gunwales were drilled for a previous fishing rod holder, which I would be covering over and reinforcing with the plate.
I prepped the surfaces by removing all paint and aluminum oxides with a flap disc (taking it down to "bare aluminum"), followed by a solvent wash.
Surfaces prepared for welding:
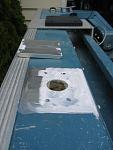
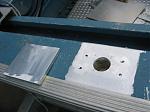
I also beveled two edges of the 3/8" aluminum plate to ease the sharpness a bit, and also make them easier to weld along those edges. I performed the beveling on my horizontal metal cutting bandsaw. Below you can see one plate ready for tack welding. Some weight is provided by the "third hand" to hold the plate firmly in position:
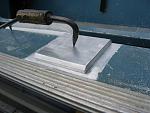
Due to existing holes drilled in the gunwales for a fishing rod holder, the cavity below being quite wet with water, there were special challenges for covering/sealing over the top. The heat of the welding would tend to boil the water in the cavity below, and the expanding steam would need to escape somewhere. If the expanding steam escaped through the weld puddle, it would cause an oxidized mess and a "blowhole". When the blowhole would form, the arc would veer off dramatically to the side (I think indicating the conductive (plasma) inert gas was being pushed away by the escaping gas/steam out of the "blowhole".) The badly oxidized blowhole area would then need to be ground away and be patched shut with a special technique.
The solution to prevent the blowholes from happening was to drill a relief hole through the plates to provide an escape path for the steam.
You can see the relief hole below in the picture of the completed weld:
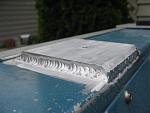
Settings used:
* 200 amps peak current, 1-1.5 second downslope (regulated current by pressing/releasing torch switch.)
* blunted 3/32" lanthanated tungsten
* minimum (20% EP) cleaning / AC Balance
* #6 gas lens w/ 15 cfh argon (provided acceptable shielding even in an outside moderately windy environment)
Note: I was a little surprised that the 200 amps, 20% EP setting gave me an "instant puddle" on the 3/8" aluminum. I was expecting i'd have to wait a little bit for the puddle to form and progress, but I actually found myself throttling the current back quite a bit with the torch switch. I used the torch switch to provide "manual pulsing", and vary the pulse duty cycle (using the switch) to regulate the power. It actually works quite well for out of position welding!
'13 Everlast 255EXT
'07 Everlast Super200P