Aluminum Boat Fuel Tank Support Structure (jakeru's #?)
[edit: this is jakeru's project #18[
I welded a fuel tank support into the hull of an aluminum boat, and a structure to raise the deck above it up higher, to provide room for the top of the tank.
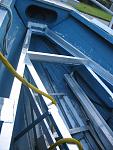
Here are the welds on the actual fuel tank support, down low in the hull of the boat. I used the torch switch at I think somewhere in the area of 180-190 amps, with 1-2 seconds of post-flow to feather the heat down where needed. Went through quite a few sticks of 1/8" 5356 filler rod on this.

C-clamps were useful for jigging up the pieces.

I cut some pieces with the horizontal bandsaw (It's a natural for cutting tubing/bar stock, such as this)
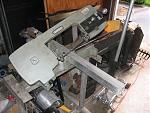
Other tools I made use of are, a 4.5" angle grinder with a flap wheel (for removing paint to prepare surfaces for welding) and also a nonferrous grinding wheel (for removing material, to fine-tune the fitment of the pieces.)
Sometimes you get creative with methods to clamp, pre-stress, and hold pieces in just the right position to get those tack welds on there. Here I used a claw-hammer and two C-clamps to pry and hold a piece into position for tack welding with both hands free (to manipulate TIG torch and filler rod.)
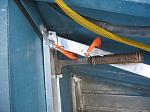
It was kind of tricky getting good vision in some spots, while crawling around in the boat hull doing this work. Sometimes I feel like I really could use a welding helmet that is tighter to my head.
(How annoying is it when you think you can see, are all ready to weld, flip the helmet down and "bump" goes the helmet - hey I can't see!) This was on a fishing boat I had done some work welding work on before.

A lot of this extruded aluminum alloy was 6061. When welding 6061 to 6061, it's important to provide a space for filler rod to be added into, to dilute the puddle and avoid hot cracking. You can see I beveled the edge of some rectangular (6061) tubing where some (6061) angle would be stitch welded to it. I did not want to build up a tall raised bead, because this structure needed a flat surface to support a deck above it.

Here is how those top surfaces turned out:
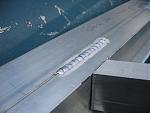
(continued next post due to 10 picture per post limitation...)
Last edited by jakeru; 07-29-2011 at 01:50 AM.
'13 Everlast 255EXT
'07 Everlast Super200P