Something remarkable I've discovered with the helium mix, at least at high penetration AC Balance settings (80% EN), is that it seems to take a lot of heat off the tungsten compared to using the same current with pure argon.
Check out the pictures below. This was a crack repair of a .6" thick lip of an aluminum, automotive wheel, which is about the thickest wheel lip I have seen in such an application. It was also a 20"x9" wheel, and further stored in below freezing shop, so pretty big heat sink that needed a lot of heat to weld... 200 amps sustained for several seconds at a time, to be precise. I did grind a vee with a carbide burr on both sides and weld both sides, as was necessary to pull this off with full penetration with anywhere near of as narrow of a weld bead as is shown.

I used the same helium mix I have been using for a few months now for a lot of my aluminum, which is, in the general ballpark mix of about 25% He. But get this... I did this with a 1/16" tungsten! Sorry I didn't take a before pic, but it started out as a truncated point, like a crayon shape. It is a 2% lanthanated. Here is what it looked like after:
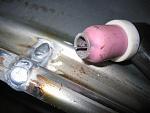
It's got some "multiple protrusions", (so is definitely pushing the current limits on it without balling it), but, what's amazing to me is, how the tip didn't melt right off and drop into the aluminum puddle, or even completely "ball" at this current level! I am almost certain if I were using pure argon at 200 amps sustained for several seconds, it would have melted at least a pretty nice sized ball, and maybe even dripped the molten tungsten tip right off. What do you guys think?
So, putting aside the benefits of the extra and penetration per amp that Helium allows, it seems like there is an additional benefit, that it allows you to run a smaller tungsten (providing further more focused, controllable, and penetrating heat on thick materials.)
End result: the crack in the .6" thick wheel, I was able to repair with full penetration (from both sides) with the Helium mix and a 1/16" tungsten, with a measured bead width of only .35", (that's just a little bit over half the thickness of the material) without really even trying that hard. I don't think that would have been possible with pure argon.
(Now in hindsight, I could have further turned up the He% to try further increasing heat per amp, and probably welded this without even needing 200 amps, but I wanted to try this thick wheel with my "usual mix" to see how the tungsten would hold.)
'13 Everlast 255EXT
'07 Everlast Super200P