Project 5 from KSmith. Category: Custom Off-Road – Log Splitter Drop Hitch
My new log splitter had a hitch point that was way too high for my 4wheeler. I had to build a drop hitch to get the splitter to the right height. I used the existing mount holes for the previous hitch which was at the same (blue) level as the two-bolt attach point.
A difficulty was to plan both distance to the clevis at the 4wheeler, and also height, considering wanting the spitter to run level. Cutting the angled tube, and fabricating the joints properly. The 4wheeler interface is 6 inches above ground level.
Materials:
Square tube mating with splitter is 1-3/4”, 1/8” wall thickness.
The Square tube an an angle is 1-3/4”, 1/8” wall thickness.
The lower horizontal square tube is 2”, 1/8” wall thickness.
The two clevis point plates are approx. 8” X 3” X ¼”.
There is a 1-3/4”X2-1/2”X3/16” plate doubler at the upper joint, horizontal to angled tube.
(bolts are 3/8”, existing from original hitch)
I used the 80 amp harbor freight inverter stick welder. Could have used more heat, but it is what I had at the time, other than a low-powered nasty northern tool flux core. Burned 5/64” 6013. If the splitter was capable of going on a road, then I would not have used this equipment setup. But for just using around my property, the design and strength are fine. The upper horizontal tube where it butts with the forward-angled tube has a doubler welded on the face for strength. The angled tube fits inside the lower horzontal tube with good welds all around. The ¼” plates were welded in two passes.
I finished the drop hitch with grey primer, and rustoleum gloss black, for easy cleanup.
The splitter tows great now, and backs easily. It is less a chore to move the splitter around by hand with the long tongue to grab. Enough room between 4wheeler and splitter now so it’s easy to get the hitch pin in place.
ken
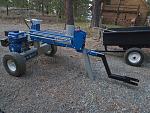

UNT 520D plasma/stick/tig; Hobart Handler 140 Mig; HF 80amp stick welder; Victor O/A; 4x6 Horizontal bandsaw; Planishing hammer; & Stuff