Someone else was careless; I was bored. 1&1/4" pin repair
Title says it all, really. There is a 1&1/4" pin that slides into a slot on the back of our fork lift. It's for light dragging as well as loading onto a vehicle using a winch. It's removable so you can use it with closed end shackles, etc. It's just hotrolled round bar with a handle welded on it. The rollback drivers often use it as a dead weight when respooling their winch lines, since using a birdsnested or otherwise FUBAR wire rope destroys it. Well, one driver didn't have the pin fully seated, and so the 8k winch bent the pin open, which made it non-removeable. I had a truck recovery early this AM, guy jack knifed in the rain, so was filthy and sweaty and soaking wet, so I didn't feel like getting into my car and going home til I air dried a little.
Anyhow, I cut the pin out with a sawzall.
As you can see, it bent pretty easily over about a 8" unsupported length; it's dead soft mild steel.

So I played blacksmith and got out the cutting torch(no rosebud around) and between hammering with a sledge and pressing in a vise, I was able to straighten it out enough. I ground it into what was basically a giant V groove, so I could get access to the entire seection of the material.
Then, I broke out the 160STH with the TIG and just started stacking the weld in at about 140amps, full power was too hot with just an on/off switch. Used 3/32" 70S2 filler, wound up extending it about 1", mostly to just wash out all the crap that I was getting off the pin.
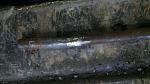
Spent about 90 minutes on it, with about 10 minutes set up time for the welder, which I keep boxed up. More work than making a new pin, but no material costs. S/F.....Ken M
Last edited by EchoSixMike; 10-14-2012 at 06:29 PM.
Lincoln Power MIG 300
Everlast 160STH
Miller 225 Thunderbolt (sold it)
Lincoln Squarewave 175 TIG(traded it for)
Miller DEL 200 welder/genset
Thermal Dynamics 1250XL plasma cutter
Miller XMT300